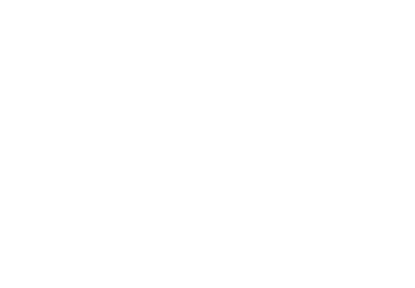
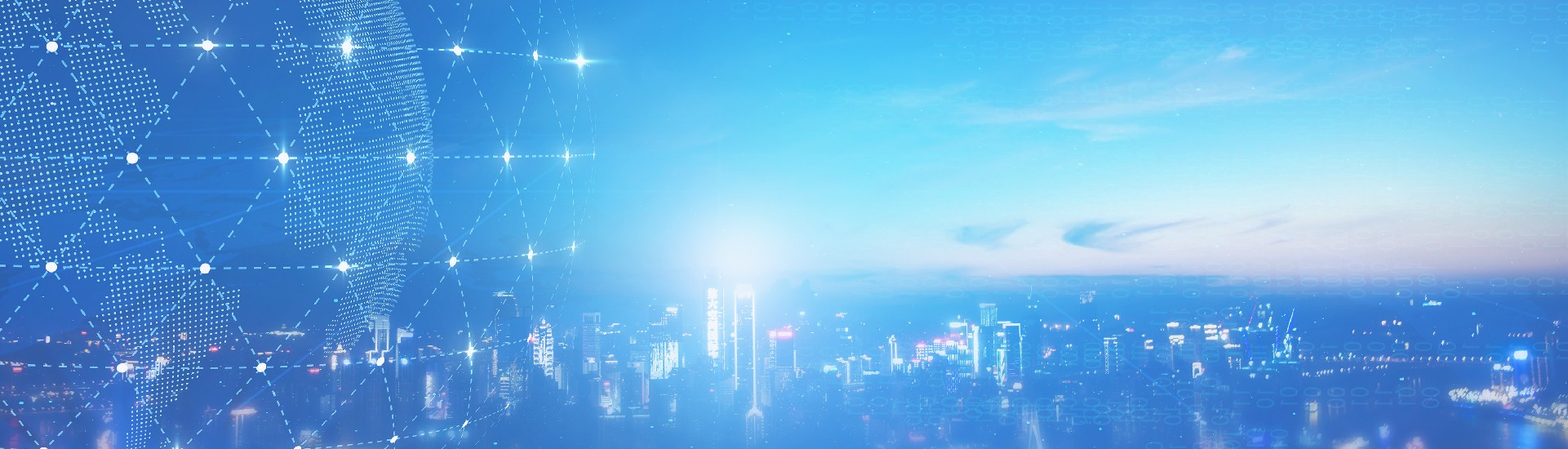
NEWS CENTER
新闻中心
硝化反应
来源:英格尔医药 发布时间:2021-08-10
硝化反应是化学工业中非常重要的一类反应,硝化反应的产物硝基化合物在医药、农药、染料、炸药等多个领域里都可以觅得其身影。硝基化合物最重要的用途即向化合物中引入氨基,或者进一步引入其他官能团,或者是形成某种杂环化合物。
硝化反应是剧烈放热的反应,依据底物特性不同,其反应热一般在120~250 kJ/mol。硝化反应的绝热温升可达150℃以上。因此釜式工艺中通常采用滴加的方式,避免反应集中放热导致飞温。
某医药中间体,原有中试工艺采用釜式间歇完成,因2018年之后硝化间歇工艺无法新建落地,采用连续流工艺尝试小试工艺开发后,反应时间极大缩短,转化率和收率均有提升。工程撬装只需要约10 m2的场地即可完成1 m3/day的生产,效率大幅提高。
反应器形式 | 反应温度(℃) | 反应时间 | 转化率(%) | 选择性(%) |
釜式 | 70 | 数小时 | 95 | 90 |
微反 | 75 | 24 s | 99.3 | 95 |
釜式工艺 | 微通道工艺 | |
产能 | 500kg/月 | 1000kg/月 |
设备 | 搪瓷釜、搅拌电机 | 碳化硅反应板、泵、仪器仪表、恒温机等 |
一次费用 | 30万 | 100万 |
耐用性 | 一般,停工维护 | 优秀,稳定生产 |
二次费用 | 因腐蚀导致的维护费用高 | 很少 |
人工 | 5人/班 | 2人/班 |
政策性 | 新建不允许采用 | 国家鼓励推荐 |
能耗 | 热效低,能源损耗大。 | 热效高,设备体积小,能源损耗小。可节省能耗至少50%。 |
单耗 | 一般 | 单耗比釜式工艺减少8.8%。 |
重氮化反应
重氮化是精细化工中很重要的一步反应,由于重氮盐的化学性质非常活泼,可发生多种反应。重氮盐与酚或芳胺可发生偶合反应生成偶氮化合物,所以重氮化是制备偶氮染料的主要过程。重氮盐中的重氮基在适当条件下可以发生多种官能团转化反应,从而可在芳环上引入羟基、卤素、氰基、巯基和肼基等取代基。
重氮化是放热反应,而且反应速率相当快。由于重氮盐不稳定,为了增加重氮盐的稳定性并避免副反应,重氮化时通常要用过量较多的无机酸,并始终保持亚硝酸钠微过量。由于重氮盐受光或受热都会分解,有些重氮盐在干燥状态受热或受震会急剧分解而引起爆炸。因此,重氮化一般要在低温下进行,制得的重氮盐溶液要立即进行下一步反应,不宜存放过久,更不宜制成干品。
采用连续流工艺,可实现重氮化反应在微通道反应器中快速均匀混合,反应产生的热量迅速移除,保证反应体系不发生飞温。系统强大的移热能力可以使得反应在比釜式反应更高的温度下完成,从而避免使用低温冷媒,减少能耗费用。
反应器形式 | 反应温度(℃) | 反应时间 | 转化率(%) | 选择性(%) |
釜式 | -5~5 | 1.5h | 98 | 84 |
微反 | 20 | 13 s | 98 | 95 |
釜式工艺 | 微通道工艺 | |
产能 | 1000吨/年 | 1000吨/年 |
设备 | 搪瓷釜、搅拌电机 | 碳化硅反应板、泵、仪器仪表、恒温机等 |
一次费用 | 600万 | 900万 |
耐用性 | 一般,停工维护 | 优秀,稳定生产 |
二次费用 | 因腐蚀导致的维护费用高 | 很少 |
人工 | 8人/班 | 2人/班 |
政策性 | 新建不允许采用 | 国家鼓励推荐 |
能耗 | 热效低,能源损耗大。冷冻盐水一次性投资大 | 热效高,设备体积小,能源损耗小。反应温度几乎可以在室温条件下,可节省能耗85%。 |
单耗 | 一般 | 单耗比釜式工艺减少10.7%。 |
重氮盐分解反应
有机氟化物在医药工业中有非常重要的应用。上市的新药中,每年大约有15-20%都是有机氟化合物。在含氟的药物分子中,通常氟的含量都比较低,每个引入的氟原子或含氟基团都有其特定的目的。有机氟精细化学品包括氟农药、氟医药、氟染料、含氟芳香族中间体、含氟表面活性剂和氟惰性流体等。
有机氟中间体主要包括芳香族氟化物和脂肪族氟化物,其中又以芳香族氟化物为主。通过芳香胺重氮化生成重氮氟盐后,控温分解是得到芳香族氟化物的重要方法,该方法采用间歇釜式操作时,由于重氮盐分解时剧烈放热,反应需要通过滴加或者缓慢升温的方式来控制分解速率,因此操作过程漫长,且有可能形成大量的焦油。
采用连续流工艺后,由于换热效率高,可将分解产生的热量有效带走,减少局部升温而产生的焦油副产。
反应器形式 | 反应温度(℃) | 反应时间 | 转化率(%) | 选择性(%) |
釜式 | 20-45 | 数小时 | 99 | 80 |
微反 | 40-60 | 120 s | 99 | 85 |
加氢反应
加氢还原反应是石油化工及精细化工中很重要的一类反应,包括各类不饱和键的加氢,如硝基化合物、醛、酮、烯烃、炔烃等,这类反应一般都是放热反应,特别是硝基化学物的加氢是强放热反应,其反应热可达500kJ/mol以上,因此采用高压釜用氢气还原硝基化合物时必须稳定控制通入氢气的速率,同时搅拌保证催化剂分散均匀,避免局部反应速率过快,热量聚集形成热点。
采用连续流方式,气固液同时进料,保证物料混合分散均匀,气固液三相具有较大的接触面积,以及相对稳定的反应接触时间。同时微通道设备具有较小的持液体积,较大的比表面积,反应热能够及时移出反应体系,从而保证过程的本质安全。同时设备的小型化也使得反应器具有较高的空时收率。
反应器形式 | 反应温度(℃) | 反应时间 | 转化率(%) | 选择性(%) |
釜式 | 50 | 4 h | 99.9 | 93 |
微反 | 55 | 1.2 min | 100 | 99 |
釜式工艺 | 微通道工艺 | |
产能 | 300kg/月 | 360kg/月 |
设备 | 高压釜、搅拌电机 | 不锈钢反应板、泵、仪器仪表、恒温机等 |
一次费用 | 600万 | 1100万 |
耐用性 | 一般 | 优秀,稳定生产 |
人工 | 6人/班 | 3人/班 |
政策性 | 新建不允许采用 | 国家鼓励推荐 |
能耗 | 热效低,能源损耗大。 | 热效高,设备体积小,能源损耗小。可节省能耗至少50%。 |
单耗 | 一般 | 单耗比釜式工艺减少3%。 |
氧化反应
反应器形式 | 反应温度(℃) | 反应时间 | 转化率(%) | 选择性(%) |
釜式 | 80 | 3.5 h | 80 | 83 |
微反 | 130 | 1.5 min | 83 | 85 |
羟醛缩合反应
反应器形式 | 反应温度(℃) | 反应时间 | 转化率(%) | 选择性(%) |
釜式 | 40 | 4 h | 98 | 60 |
微反 | 80 | 2 min | 98 | 74 |